VMT PickFinder 3D
Reliably detecting, gripping and moving
VMT PickFinder 3D reliably detects individual objects in sorted and unsorted scenarios. It determines the coordinates for safe gripping and calculates the optimal path of the gripper arm to the object and to the subsequent processing location. Intelligent collision avoidance guarantees stable process reliability.The straight path is not always the shortest
In many processes, the gripper arms of robots and handling machines are controlled using target coordinates: They move on a straight path from point A to point B. However, even in an only moderately complex situation, the straight path may be unsuitable. Objects that protrude inward or outward may become an obstacle. This also applies to the contour of the gripped component itself.
It is impossible to pre-program all eventualities in chaotic situations. The path to the object, the detection of the safe gripping coordinates and the path to the next station can be completely different for each process. An optimal process – reliable, collision-free and fast – can only be achieved through individual, situation-related control.
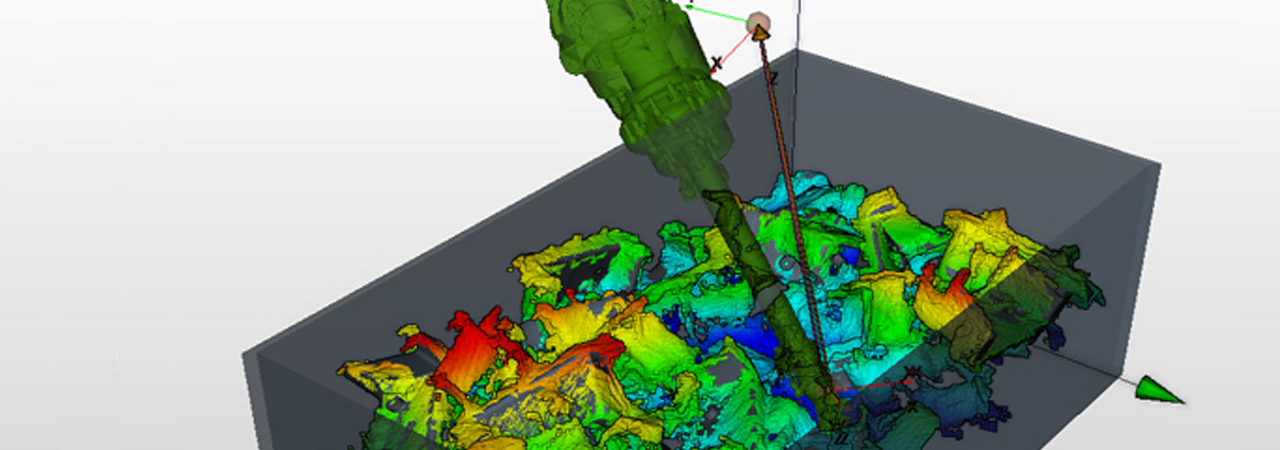
The solution: Image and data
At the beginning of the picking process with PickFinder3D, the optical sensor takes a 3D image of the component scenery. The raw data of the recording are preprocessed by the PickFinder software. It filters and compresses them into an optimized data set. This is used by the intelligent search algorithm to identify a suitable target object. The object was previously taught in by the setup assistant of the PickFinder 3D. It can be scanned in directly by the system or represented by a CAD file.
Safe handling thanks to the multi-point track
Based on the optimized data, PickFinder3D prioritizes the parts according to their grip attractiveness. It is based on application-specific parameters such as accessibility, completeness of access and freedom from collisions on the path there and back.
The gripper arm moves on the optimal – but not necessarily straight – path to the gripping point and set-down point. PickFinder3D gives it a multi-point path that takes all obstacles into account and circumnavigates them. Starting and extending are reliably carried out without collision.
Containers in view
The position of the component container is also recorded by the system. Its contours, including fluctuations in the position of the container or deformed outer walls, are included in the trajectory calculation. The container doesn’t require a complex fixation. Position variations and shape no longer lead to a risk of collision.
A major advantage for overall efficiency
The PickFinder 3D technology achieves a very high degree of reliability throughout the entire process. Optimal travel routes enable short cycle times. Incorrect grips and collisions are practically impossible. Gripper-related downtime is avoided, which often significantly increases overall efficiency.
Practice
Sensor-independent:
PickFinder3D can be coupled with any 3D sensors.
The optimal sensor is selected for each application.
Setup assistant:
An intuitive setup assistant helps teach-in the components and their gripping points.
Parameters:
PickFinder 3D provides the user with a broadly diversified parameter field in order to perfectly adapt the system to the application.
Flexibility:
The parts do not have to be homogeneous. PickFinder3D can also distinguish and handle different components in the same scenery.
Application level:
Several levels are available to the user to work with the software, which are differentiated according to application knowledge. He can decide whether the basic functions are sufficient for him or whether he wants to use the full range of parameters. Almost every menu function can also be activated or deactivated for individual users.
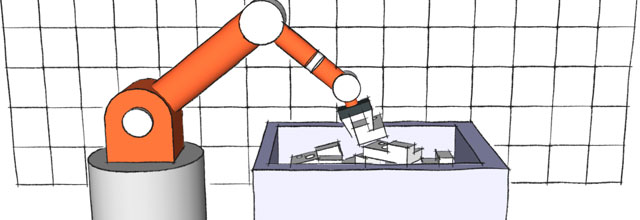
An entire system from a single source
Automated component removal is a complex process in many processes. This is especially true of unsorted, chaotic parts deliveries.
VMT offers competent solutions from a single source:
Careful system design, precise adaptation to the application and detailed parameterization provide enormous advantages: Once the system has been set up at this level, the company will benefit from trouble-free operation.
VMT takes care of the design and adaptation in close cooperation with the customer. We ensure that PickFinder 3D is perfectly tailored to your process in all aspects – from the selection of sensors and grippers, to installation, parameterization and commissioning.