VMT SpinTop
Available from March 1, 2024: Next Generation - VMT SpinTop G2
Faster, more precise, more efficient – modern adhesive bead inspection with VMT SpinTop G2. The completely redesigned laser modules and optical blocks now provide triple the sampling rate at double the resolution.
With the SpinTop G2 transitioning to Class 2 visible lasers, the sensor has a wider spectrum to work with while still providing excellent stability in varying lighting conditions and dark surfaces. The sensor uses a combination of red and blue lasers to allow simultaneous acquisition at high frame rates. This results in new application possibilities and an overall optimized detection process.
With existing installations and maintenance in mind, the new SpinTop G2 sensor will maintain the same mounting and cable connections as the current SpinTop. VMT has also ensured that the new SpinTop G2 sensor family will cover the same field of view and operating distances as the current SpinTop sensor selection. These considerations will make future upgrading or retrofits of existing systems nearly effortless.
VMT SpinTop 3D
The VMT SpinTop 3D revolutionizes current technical standards and is tailored to the demands of first-class adhesive bead checks. The optimum use of infrared laser technology in connection with robust analysis algorithms guarantees reliable quality checking for adhesive beads.
An important issue: sustainability
In addition to its high performance and precise quality control of adhesive beads, the VMT SpinTop 3D also excels in terms of sustainability.
Why? With the SpinTop system, the adhesive seam can be directly inspected during the adhesive application without any loss of cycle time. This means that it is already clear before installation whether scrap is being produced or not. As a result, a reduction in scrap is possible. Additionally, energy is conserved by reducing the power consumption of complex inspection facilities downstream.
The sensor head, which moves independently of the glue nozzle, allows the entire adhesive bead process to be measured. The transmission path for energy and data between the fixed and the rotating part of the sensor head is designed to be entirely non-contact and maintenance-free in order to reduce wear and tear to a minimum.
Measurement distances can be selected on a flexible basis, and cumbersome parameterization and calibration procedures are not required. All measurement results can be documented specifically for each vehicle, and can be visualized on the VMT user interface in a clear and self-explanatory manner.
- Direct and earliest possible detection of errors during the glue application process
- No reworking costs due to incorrect glue application in subsequent work steps
- Comprehensive checks make it possible to cut down on possible previous glue overdoses.
- Cycle time savings through inline measurements directly during the glue application
- Simple retrofitting of existing systems; existing system processes remain the same
- Optimum positioning of measurement technology, since the VMT SpinTop 3D is mounted „around“ the glue nozzle
- Minimum interference contours due to compact design
- Customer specific detailed logging - each individual result can be displayed
- Only turn-on and turn-off signals (triggers) must be added to existing robot programs
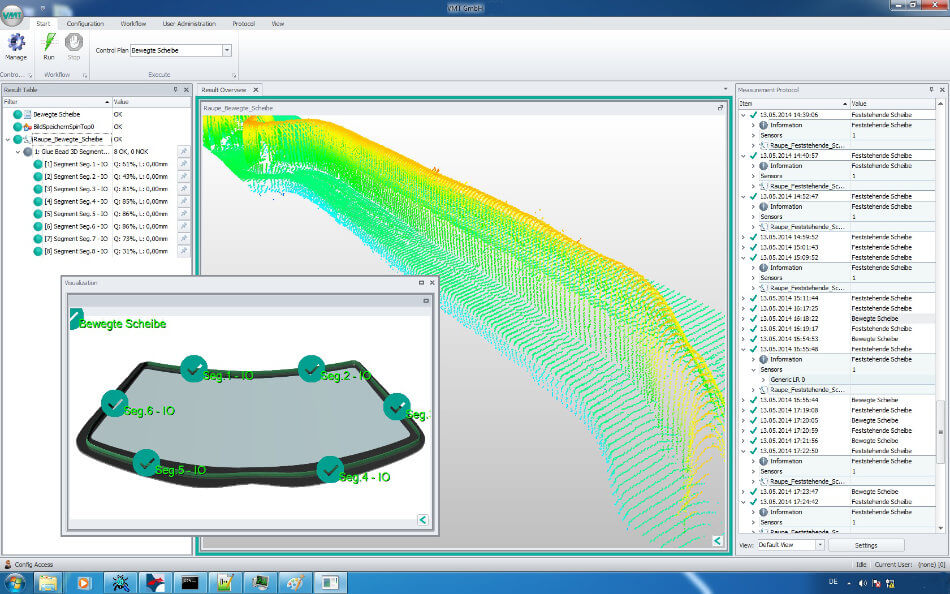
Features
- Full three-dimensional check of adhesive bead with regard to width, height, continuity and geometry
- Online detection parallel to adhesive bead application
- Resistant to color and contrast changes, different surfaces and reflections
- Independent of the glue color - can be changed without new sensor parameterization
- Flexible measurement distances can be set for the respective glue nozzle lengths
- Two measurement units for optimum capture of 3D geometry
- Free segmentation of test parameters and tolerances
- Freely programmable and robot-independent rotation of sensor unit
- Separate rotation axis for direct inline measurements
- Non-contact, maintenance-free energy and data transmission
- Technology package for communication with robot
- Minimal set-up requirements since the rotations do not have to be programmed
VMT SpinTop 3D - robot-guided or permanently mounted
The VMT SpinTop 3D is mounted directly on the glue gun. The unit can then be guided along the work piece by a robot or it can be used as a stationary version. In the second example, the robot moves the work piece underneath the glue unit. The freely programmable rotation of the sensor unit means that the measurement range can always actively follow the application path.
Installation on the robot wrist joint is risk-free due to non-contact data and energy transmission. Broken cables or wear and tear of friction rings can be excluded. The VMT technology package installed in the robot guarantees the exact tracking of the adhesive beads.
Exact path check of the glue beads is also possible with a VMT SpinTop 3D that is installed on an existing application unit thanks to the online connection to the robot. The rotation is controlled directly by the VMT system. This does away with the separate set-up of a measuring run.
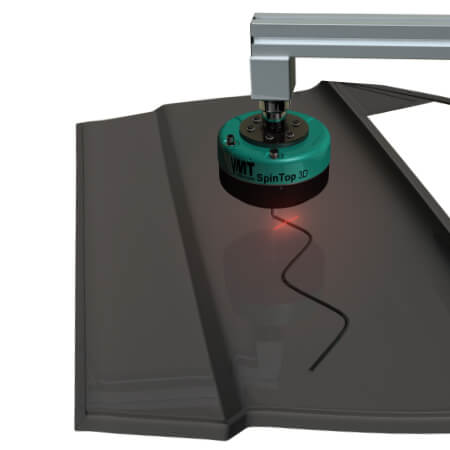
Online adhesive bead check
- Weight approx. 3 kg
- Diameter of installation opening 45.0 mm
- Measurement distance / Measurement range
Xmin = +/- 15 mm
Xmax = +/- 21,5 mm
Z = 35 mm ...110 mm - Infrared laser, class 1
- Operating voltage 24 V DC,
- Power consumption max. 50 W
- Ambient temperature 0 ... 40 oC (32 ... 104 °F)
- With heated application nozzle, max. heating temperature 60 oC (140 °F)
- Connections for supply voltage and data transmission per TCP/IP
- Protection type IP42
- Angle of rotation, endless
- Sampling rate 300s-1